10.04.2025 | Clients
Effizienz trifft Vielseitigkeit
By Tobias Krist, HURCO Sales
“The simple, fast programming for small series and individual parts with the HURCO control on it. That has given us advantages.”
Markus Dettendorfer, owner Dettendorfer Maschinenbau GmbH
Today we are introducing a customer who has established a rather unusual business model for contract manufacturing. Dettendorfer Maschinenbau combines various manufacturing methods and unites sheet metal processing, machining and, since 2015, laser welding to cover a flexible range of orders. This combination makes it possible to manufacture even large components efficiently.
Machining with seven HURCOs
Dettendorfer’s production hall is equipped with seven HURCO machines for machining. 30 employees, almost all master craftsmen or technicians, use their skills here. Most of them were also trained in the company – a practice that has been followed since 1998. This has resulted in a team with five specialized production groups: Turning, milling, plate and sheet metal processing and joining.
“We currently have seven HURCOs. Most of them run 40 hours a week. Basically, this running time is only limited by the availability of employees.
Precision and versatility in production
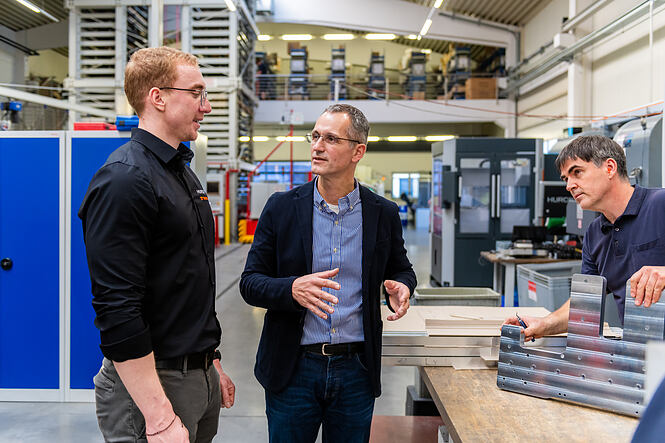
Dettendorfer manufactures components ranging from simple covers to precision parts. Dettendorfer is also successful in special machine construction. And here the tolerance limit is usually in the hundredths. The thermal stability of the machines is also particularly important to Dettendorfer because a lot of work is done with aluminum. It accounts for around 50% of the material used. Stainless steel accounts for a further 20 % and steel, non-ferrous metals and plastics for the remaining 30 %.
WinMax control system and efficient processes
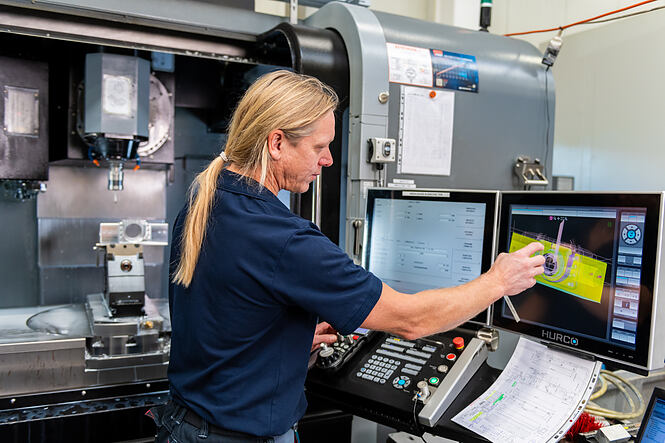
Our WinMax control is appreciated by operators because it makes programming the machine easy. Dettendorfer’s customers usually supply 3D data, but if this is incomplete or not available at all, WinMax helps to implement the programming quickly and easily. This also applies when a workpiece comes from sheet metal processing and details still need to be milled. In this way, Dettendorfer now even manufactures some products itself that were previously bought in. One example: Dettendorfer used to source pistons for steam engines externally. After several problems, the company decided to manufacture them itself. Although the measurement and optimization of the pistons was initially time-consuming, the HURCO machines subsequently enabled a clean implementation. Since Dettendorfer has been manufacturing the pistons in-house, the components not only fit better, but also last twice as long as the previous purchased cast variants.
Automation as the next step
“Thanks to the process-reliable solution, we can machine up to 36 components on multiple sides overnight.”
Previously, the machines at Dettendorfer only ran during working hours. A new automation solution now enables night-time production – without robots. Up to 18 part-equipped vices (150 mm x 150 mm) are processed automatically overnight, allowing 36 additional components to be produced. Thanks to the open interfaces of the HURCO machines, this automation could be easily integrated. Further integrated automation with HURCO technology is now also planned. We are looking forward to it.
“The machines have increased our competitiveness. They have brought us forward both technically and economically.”