03.11.2023 | Clients
HURCO is the reason our business model works in the first place
“We can produce parts for classic models and for motorsports vehicles even if the parts don’t exist anymore. And we can do it in just a few hours,” said Philipp Fischer to describe the business concept of Westwood Performance. To sum it all up, “We specialize in historical sports cars, and our main focus is drive technology.” Maximum flexibility is the top priority at this company in Gebhardshain, Germany, due east of Bonn. To support this priority, they use a 3- and a 5-axis machining center from HURCO.
The whole thing started with Fischer’s passion for vintage motorsports. He started out building his own cars, followed shortly by orders from customers. “Today, we work with the classics as well as current models of sport and performance cars. The ‘treasures,’ though, are the foundation of our business model,” indicated the CEO. The team includes four jack-of-all-trades types with extensive expertise and a strong passion for automotive sports. The team members have backgrounds spanning from classic automotive mechatronics technician to master mechanic and machine shop foreman. What they share is enthusiasm for older and historic cars. The machine fleet in their shop includes a simple tire changer, CNC lathes and milling machines. They also have specialty equipment for engine work, such as honing machines, at their disposal. To supplement an older HURCO BMC30, a 3-axis machine, they purchased a 5-axis VC 500 i from Pliening, Germany about a year ago.
Making spare parts that don’t exist anymore
Fischer explained how they work with the 5-axis machining center: “Sometimes when working on an engine, we bore out the cylinder barrels with the VC 500 i and then hone them. Generally, however, we produce complete parts using both HURCO machines. Our only day-to-day business is engine construction and differential technology, because of the recurring wear parts for motorsports. The rest is custom parts and components for cars from the 50s and 60s. They’re no longer off-the-shelf items, so they need to be custom produced.”
Although Westwood produces parts for the classic car restoration and motorsports companies, Westwood is primarily active in the private sector. “This means we have great responsibility for the quality of our work,” Fischer emphasized. “After all, racing with historical sports cars stresses the technology to the maximum degree.” Westwood also currently sees potential in the production of spare parts with an operating permit for popular classic cars. “Demand for spare parts is increasing. A market that we can serve economically with our two machining centers is opening up,” Fischer confidently said.
Cross-model components by customer request 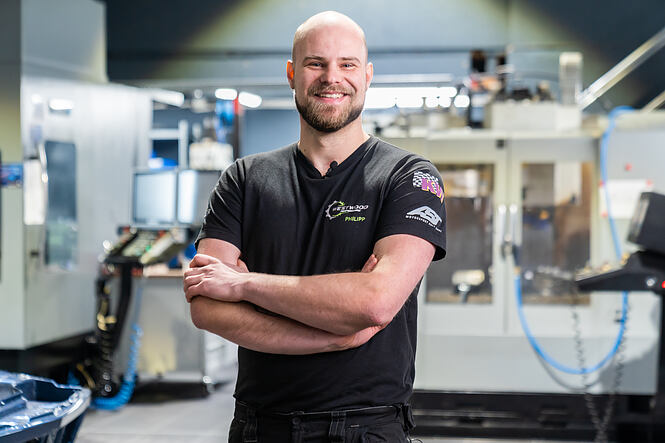
However, he isn’t only talking about 1:1 replacements. They also make parts from different materials, including novel ones, that substantially improve performance. “We also design parts from scratch. For instance, when a car was rebuilt and certain configurations are no longer compatible,” explained Fischer. “At the same time, the VC 500 i offers us entirely new possibilities. It enables us to produce one-offs, small series runs, or model-independent components by request. These options didn’t exist 60 or 70 years ago.” For instance, Westwood can now offer parts that would otherwise never have made their way onto the streets, like parts for the DTM racing series. And they can also produce completely new components designed in collaboration with an engineering firm.
Parts for motorsports must fit perfectly
In all this variety of parts, the top priority is maximum flexibility. “That’s also the reason we went with the VC 500 i,” Fischer said. “In order to be competitive with what we offer, we have to provide numerous machining processes in a limited space. With its 5-axis capability, the VC 500 i is perfect for us. Simply put, it enables us to machine all the parts in our portfolio.” To machine workpieces up to 625 mm in diameter that weigh up to 250 kg, the machining center is equipped with a 13-kW spindle rated for 12,000 rpm, a SK40 interface, a swivel table, and a tool changer with 30 positions. “Our parts are generally so complex that we have to prepare them in a separate CAD/CAM system,” the CEO continued. “Data then go directly to the machine, whereby the MAX5 control system works in perfect harmony with the CAD/CAM system.”
Intensive simulation takes place before machining. Features such as AdaptiPath for trochoidal milling or UltiMotion for high-speed machining could be interesting for the future. “In that sense, we can still tap lots of potential with the machine,” Fischer said confidently. Manufacturing accuracy is generally in the hundredths range. However, according to the CEO, there are also parts with tolerances in the visual inspection range. That’s typical of classics. “We now manufacture interfaces or guides that were originally produced by hand with as much accuracy as possible. And in any case, parts for motorsports have to fit perfectly.”
Flexible availability of parts for historical sports cars
“We are very satisfied with the VC 500 i,” said Fischer. “It offers exactly the flexibility, robustness, and quality we need for our parts. Together with the control system, it’s a package that comes at a very attractive price.” In-house manufacturing processes needed to improve in terms of flexibility and quality as well as safety and simplicity. That’s why Fischer “could only consider a machine that’s easy to operate.” He also feels validated in his decision based on “HURCO’s good service, in which we were interested.” This was clear early on when they met with Horst Mumper, “who really impressed us in his role as a commercial-technical consultant. Following our initial research, we only had a vague description of our specifications.”
What followed was a comprehensive consultation session on the different machine concepts. “Two days later, Mr. Mumper joined us at our shop. He spent hours measuring and weighing every part and every engine. He took a look at our machines and got a feel for our requirements. Quite simply, it was clear to us that we were in good hands.” Mumper added: “During my visit, we discussed every contingency that could arise. Unlike most tuning shops, which outsource milled parts, the main motivation at Westwood was maximum flexibility in the availability of parts for historical sports cars. With the company’s imaginative power and decisiveness, we led the HURCO machines to visible success.”
The customer takes notice
The endeavor’s success is plain to see in the increased number of incoming orders that Westwood can now process on the new machines: “Our new 5-axis capability is one part of the equation. The other part is that the VC 500 i considerably increases our capacity. In our day-to-day work, it means having the 5-axis accessibility that is necessary for our structural parts. Our new equipment also means transformer-free machining.” That being said, parts are also pre-machined on five sides so the last side can then be processed on the 3-axis machine. In this workflow, the control systems accept the data seamlessly. “In summary, we now have a very economical operation and are considerably more competitive than before. That’s especially true because the VC 500 i also operates autonomously. This gives us a moment to drill a bushing or cut a crown wheel. Plus, the machines can run through the night, which is a big help to our small team.” The ability to produce parts that don’t exist anymore has long been the key to success. This will exponentially expand in the future. “Today, we can already accept, modify, and ship out a differential on a Friday afternoon. That makes a real difference in terms of competitiveness and will yield lasting success. Because the customer takes notice.”